Il turbocompressore ha subito una notevole trasformazione nel corso del tempo. L’interesse dei progettisti di motori si è concentrato sempre di più su questo componente, esso ha permesso un notevole abbattimento dei consumi e delle emissioni, associato ad un incremento di prestazioni. A questi vantaggi si è accompagnata una riduzione della cilindrata volumetrica del motore (il tanto di moda downsizing).
Un moderno turbo di rotazione necessita di un controllo su banco di prova
Il particolare interesse dedicato ai turbocompressori ha permesso di ottenere motori più leggeri, economici e prestanti; anche se questa evoluzione tecnologica ha complicato di molto l’attività del ricostruttore di turbo. Difatti, sono sempre più frequenti casi in cui un turbocompressore che, apparentemente revisionato a regola d’arte, una volta montato sul veicolo mostra tutti i suoi limiti. Difetti che si traducono in uno scarso o inaccettabile rendimento del motore.
L’unità di controllo del motore è diventata più esigente
Le cause di questa situazione sono evidenti da comprendere: rispetto al passato, le prestazioni del motore poggiano sempre più sul turbocompressore e quest’ultimo è chiamato ad avere parametri contenuti in un ristretto campo di tolleranza. In altri termini, se in passato il controllo visivo del turbocompressore era sufficiente perché il motore accettava di buon grado un turbo fuori specifica, oggi è necessario un controllo strumentale che ci consenta di misurare le effettive caratteristiche del turbo.
La risposta alla evoluzione tecnologica nel mercato After Market
Per far fronte a questa nova esigenza, i costruttori di macchine per la riparazione o la ricostruzione dei turbocompressori hanno introdotto sul mercato diverse soluzioni che possiamo suddividere in due grandi famiglie: il banco di flussaggio dinamico ed il banco di flussaggio statico.
Un richiamo sul funzionamento del turbocompressore
Prima di addentrarci in un’analisi di pregi e difetti delle due famiglie di macchine, quindi nell’oggetto di quest’articolo, è necessario fare un breve richiamo sul funzionamento del turbocompressore, con particolare riferimento ai cosidetti turbo a geometria variabile. Questo tipo di turbo è quello che più necessita della verifica sul banco.
In estrema sintesi possiamo dire che il compito di un turbocompressore è quello di incrementare la pressione dell’aria immessa nella camera di combustione. L’innalzamento della pressione, aiutata anche dal successivo raffreddamento (intercooler), permette di immettere in camera di combustione una massa d’aria superiore a quella immessa lavorando alla pressione atmosferica. Quindi, a parità di volume della camera di scoppio (cilindrata del motore), una maggiore massa d’aria, che si traduce in una maggiore coppia motrice e più elevata potenza del motore.
Inoltre, si ottiene anche un maggior rendimento del motore, che dal punto di vista dell’utente si traduce in ridotti consumi di carburante. Difatti, il lavoro necessario a comprimere l’aria in aspirazione viene fatto prelevando energia dai gas di scarico che lasciano la camera di scoppio ancora con una elevata entalpia. Entalpia che invece viene sprecata nei motori aspirati. A voler essere rigorosi, i motivi che permettono un maggior rendimento del motore sono anche altri, ma qui vengono tralasciati perché secondari per l’argomento trattato.
Se un turbocompressore sfrutta l’energia dei gas di scarico, come abbiamo visto, risulta plausibile che il suo dimensionamento passi attraverso i valori di flusso (kg/h) dei gas di scarico del motore.
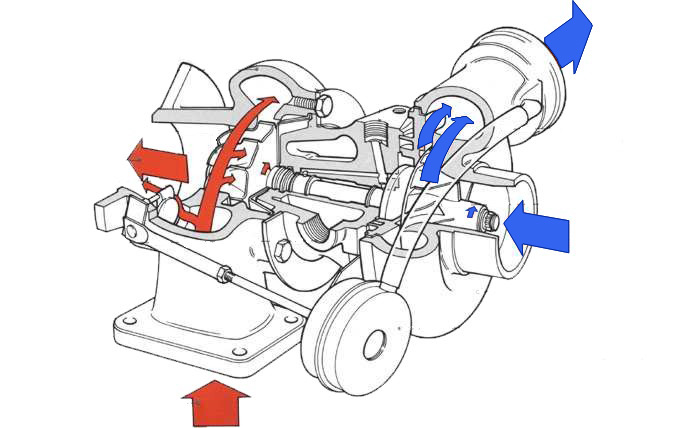
Proprio quest’aspetto introduce le prime difficoltà che si sono dovute affrontare per ottenere un efficiente accoppiamento fra motore endotermico e turbocompressore. Mentre il flusso dei gas di scarico ha valori distribuiti in un ampio intervallo, si va dal regime di rotazione con motore al minimo e senza carico agli alti regimi con elevata richiesta di coppia, il turbocompressore (quello tradizionale fig.1) è efficiente, nel senso che incrementa le prestazioni del motore, solo in un più ristretto intervallo dei valori di flusso.
Un turbocompressore con una girante di piccole dimensioni (e quindi un diffusore piccolo) lavora bene e genera incrementi di coppia del motore già con bassi flussi. Ad alti regimi di rotazione, tuttavia, proprio le dimensioni ridotte del diffusore costituiscono un’ostruzione alla via di fuga dei gas di combustione che penalizza di molto le prestazioni del motore, fino a portarle su valori più bassi rispetto ad un motore aspirato.
Per rigore espositivo è opportuno ricordare che una turbina piccola, se alimentata con forti flussi, presenta limiti tecnologici che qui trascuriamo perché inessenziali ai fini della trattazione dell’argomento di quest’articolo. Quello che qui è importante sapere sul punto è che il turbo è dotato di una valvola di bypass, detta wastegate, che devia parte dei gas di combustione direttamente allo scarico quando il flusso di quest’ultimi diventa troppo elevato per le dimensioni del turbocompressore.
Un turbocompressore con una girante di dimensioni abbastanza grandi da non creare una fastidiosa contropressione allo scarico della camera di scoppio, permette di incrementare le prestazioni del motore ai carichi elevati. Risulta però del tutto trasparente ai bassi regimi, quando il flusso non è ancora sufficiente per portare in rotazione il rotore del turbocompressore.
In definitiva, il dimensionamento di un turbocompressore a geometria fissa è sempre una soluzione di compromesso fra il guadagno di potenza massima e l’incremento di coppia ai bassi regimi. Tipicamente la scelta è sbilanciata verso l’incremento di potenza massima, quindi un motore con alti valori di potenza specifica ma modesti valori di coppia ai bassi regimi. Configurazione che nell’uso stradale si avverte con un ritardo nella ripresa ai bassi regimi di rotazione.
La soluzione a questo problema è arrivata con il turbo a geometria variabile (VNT o VGT). Il turbo a geometria variabile funziona bene sia con bassi che con alti valori di flusso. L’innovazione introdotta da questo nuovo modello di turbocompressore consiste in un diffusore turbina che non è più continuo, ma costituito da una serie di ugelli il cui angolo di incidenza e la cui sezione degli orifizi possono essere variati dall’esterno (fig.2).
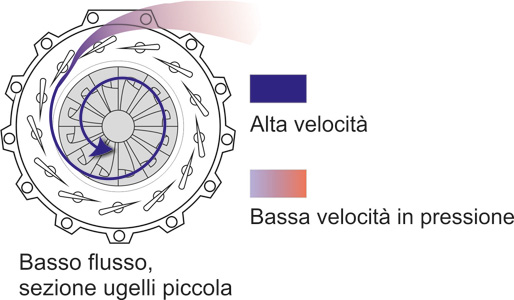

Per bassi flussi la sezione degli ugelli viene ristretta, questo garantisce comunque un’alta velocità (energia cinetica) ai gas di scarico quando lasciano il diffusore per impattare sulle pale della girante turbina. Così il rotore raggiunge una velocità sufficiente a comprimere aria dal lato compressore. In termini fluidodinamici, la strozzatura degli ugelli genera una modesta contropressione a monte della turbina evitando la perdita di entalpia del gas già all’uscita della camera di scoppio. L’entalpia viene invece persa sulla girante turbina, parte, in cambio di lavoro usato per comprimere aria nel condotto di aspirazione del motore.
Man mano che il flusso aumenta viene aumentata anche la sezione degli ugelli e il loro angolo di incidenza, che da tangenziale passa a radiale. L’aumento della sezione degli ugelli mantiene la contropressione allo scarico a valori tali da non compromettere le prestazioni del motore e, contemporaneamente, una velocità dei gas di scarico adeguata a far lavorare il turbocompressore in accordo con il regime del motore.
Alla massima apertura, gli ugelli sono disposti quasi radialmente rispetto alla girante turbina, cosi si evita contropressione e il gas di scarico fluisce producendo una contenuta coppia sul rotore. La posizione di massima apertura equivale all’apertura della valvola wastegate nel turbocompressore a geometria fissa. Valvola, che come abbiamo visto, non è presente nel turbo a geometria variabile.
Come viene scelta la posizione della geometria ai vari regimi del motore
I moderni motori vengono gestiti da una unità di controllo elettronica ECU (Electronic Control Unit). La ECU basa il suo funzionamento su mappe di parametri (map based) o modelli matematici (model based) che mettono in relazione le caratteristiche del compressore (flusso e rapporto di compressione) con il flusso dei gas di scarico e la posizione della geometria.
Un errore nella regolazione della geometria, ma anche un errore dimensionale delle giranti o dei carter o altri errori costruttivi, fa sì che il modello o la mappa della ECU non rappresenti più la situazione effettiva del motore.
Ogni differenza fra le caratteristiche del turbocompressore attese dalla ECU e quelle reali, trae in inganno la stessa ECU che non potrà gestire il motore nel modo più efficiente in termini di prestazioni e di rendimento.
Man mano che ai motori sono state richieste maggiori prestazioni, maggior rendimento e ridotti livelli di inquinamento, le ECU sono diventate molto più esigenti e tollerano sempre meno scostamenti dei parametri del turbocompressore rispetto ai parametri di targa. Per questo motivo ai moderni turbocompressori vengono richieste prestazioni contenute in tolleranze sempre più ristrette e non è un caso se la leva della geometria che prima veniva comandata con un attuare pneumatico adesso è comandata con attuatore elettronico (o pneumatico con feedback di posizione elettrico).
Oggi un turbocompressore con parametri fuori tolleranza comporta un cattivo funzionamento del motore che si manifesta con scarse prestazioni e elevati consumi nei casi più lievi, fino ad arrivare all’accensione della spia di malfunzionamento motore nei casi più gravi
Quanto è importante la corretta taratura dell’attuatore del turbo
Se il vecchio, collaudato ed economico attuatore pneumatico è stato sostituito un costoso e complesso attuatore elettronico, è solo perché la posizione della geometria è diventato un parametro cosi critico da non tollerare più l’errore presente nell’attuatore pneumatico.
Analogamente, non sono tollerabili tarature dell’attuare della geometria effettuate in maniera più o meno empirica con controlli visuali (spazio fra le palette a minima apertura e depressione nell’attuatore a fine corsa). Se si considera che il registro dell’attuatore è sempre necessario quando si assembla, o ri-assembla, un turbocompressore, si capisce bene l’importanza di uno strumento che possa agevolare questa operazione.
Banco flussaggio
Abbiamo visto che la ECU del motore ha una mappa delle caratteristiche del turbocompressore in funzione della posizione dell’attuatore. Ipotizzando che il turbo sotto esame sia del tutto identico a quello di primo impianto (stesse dimensioni e profili di giranti, diffusori, geometria, ecc.), sarà sufficiente il corretto registro dell’attuatore (relazione fra il segnale ricevuto dall’attuatore e l’angolo delle palette della geometria), perché il turbo risponda alle attese della ECU e il motore lavori nelle giuste condizioni.
Considerato che la geometria di un turbo costituisce un’ostruzione al deflusso dei gas nel carter turbina e che quindi, data una differenza di pressione, il flusso dei gas sarà funzione dell’angolo delle palette (sezione degli ugelli) si può determinare l’angolo delle palette, nota la differenza di pressione a monte e a valle della turbina e misurando il flusso di gas che attraversa la stessa.
Banco flussaggio dinamico TurboTest
Il banco di flussaggio tradizionale è un valido strumento per una corretta riparazione/ricostruzione di un turbo, nondimeno non può mai garantire che il turbocompressore sotto misura abbia le stesse caratteristiche di un turbo di primo impianto, le stesse di quelle memorizzate nella ECU. Esso ci assicura invece solo la coerenza fra segnale all’attuatore e angolo delle palette. Anzi, anche la coerenza fra segnale all’attuatore e angolo delle palette, è garantita solo in assenza di trafilamento, come vedremo.
Il banco di flussaggio dinamico va oltre, non solo mette in relazione il flusso lato scarico con il comando inviato all’attuatore, ma verifiche anche il numero di giri del rotore e la cosa più importante: il rapporto di compressione ottenuto lato aspirazione.
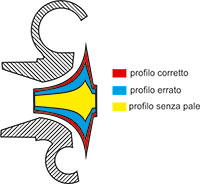
Solo una verifica del rapporto di compressione per diverse posizioni della geometria può garantire il corretto funzionamento del turbo.
Per rendersi conto di quanto sia importante il rapporto di compressione e di come possa essere parziale la verifica sulla relazione flusso lato scarico-posizione dell’attuatore, ipotizziamo una condizione estrema in cui un turbocompressore venga assemblato con una girante compressore liscia, priva di palette (giallo in fig. 3). In questo caso è evidente che il turbocompressore non potrà produrre pressione lato compressore, tuttavia una prova sul flussometro statico lo caratterizzerò come turbo in specifica. Difatti, abbiamo visto che il flussometro tradizionale misura solo il flusso lato turbina e controlla la sua corretta relazione con la posizione dell’attuatore, ma non si preoccupa di verificare se il turbo comprime l’aria in aspirazione del motore.
Nel caso ipotizzato, di assenza della girante compressore, è evidente che il motore funzionerà come motore aspirato e che la ECU segnalerà l’anomalia come guasto motore. Quando è la girante compressore, invece, ad avere una misura sbagliata (blu in fig. 3), l’effetto è lo stesso, solo di dimensioni più contenute. In aspirazione non si riesce ad ottenere la pressione attesa dalla ECU con conseguente scarso rendimento, alti consumi e, nei casi più consistenti, una segnalazione di anomalia motore. Analogo discorso vale per un cattivo accoppiamento o misure errate di carter e giranti lato turbina e in caso di trafilamento dei gas di scarico lungo l’anello della geometria.
Quanto incide una fuga di gas dall’anello della geometria
La fuga dei gas di scarico dal percorso desiderato e che quindi attraversano la turbina senza compiere lavoro, è un caso particolare, frequente, molto insidioso e merita una trattazione a parte con l’aiuto di un esempio pratico.
Abbiamo visto che il turbo a geometria variabile fa un enorme passo avanti rispetto al turbo tradizionale, questo proprio grazie ad una serie di ugelli che convogliano i gas di scarico con velocità e angolo tali da ottenere il massimo rendimento. Quindi, è importante sapere se proprio tutto il flusso passa attraverso gli ugelli della geometria, o se una quota non trascurabile riesce a sfuggire per altri percorsi (trafilamento).
Il lato turbina di un turbocompressore è soggetto a temperature e gradienti di temperatura elevati, questo, insieme al fatto che vanno accoppiati fra loro materiali diversi, fa sì che sia necessario un certo gioco negli accoppiamenti e quindi inevitabili trafilamenti.
Per un turbo nuovo, con componenti dimensionalmente identici a quelli di primo impianto, questi trafilamenti sono contenuti. Tuttavia dobbiamo presupporre che non siano proprio trascurabili, è sufficiente osservare che di recente i costruttori di turbo prestano sempre più attenzione al contenimento di queste perdite (vds. IHI ENGINEERING REVIEW VOL. 44 NO.2 2011.)
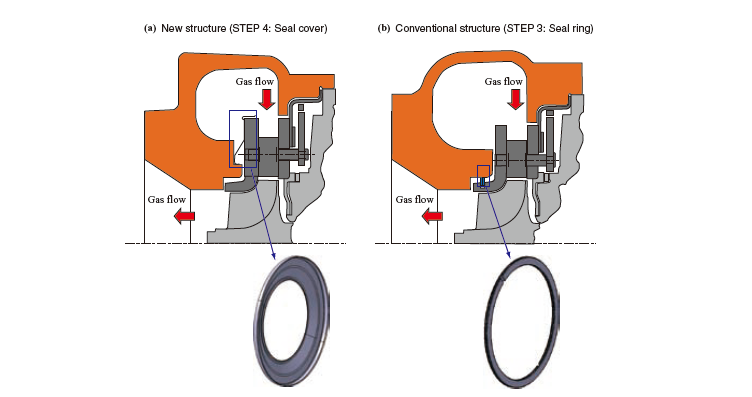
Se i costruttori di turbo decidono di complicarne la struttura proprio per contenere i trafilamenti, evidentemente la quantità di gas disperso è diventato un aspetto critico. Trascurare il valore di gas disperso, che rimane una variabile con una forte connotazione aleatoria in un turbo ricostruito, non più tollerabile in un turbo moderno, come abbiamo visto.
Per verificare quanto questo possa influire su un turbocompressore, abbiamo volutamente interposto uno spessore di 0,1 mm sui rulli della geometria. Una difformità (0,1 mm) rispetto al prodotto di primo impianto che sarebbe passata del tutto inosservata, ma che, come vedremo, compromette seriamente la funzionalità del turbocompressore.
Geometria con simili difformità sono assai diffuse sui ricambi reperibili sul mercato e non solo fra quelli caratterizzati da un basso prezzo.
La prova è stata condotta assemblando un turbocompressore con tutti i componenti corretti, si è proceduto al registro della geometria, alla misurazione del flusso lato scarico (come succede nel flussometro tradizionale) e quindi si è passato alla verifica del rapporto di compressione lato aspirazione (prova possibile solo su un flussometro dinamico). Registrata la geometria anche il rapporto di compressione e il numero di giri risulta contenuto nei valori di specifica (v. tabella 1).
Allo stesso turbocompressore è stato inserito uno spessore di 0,1 mm sotto i rulli della geometria (simulando una difformità dimensionale dei soli rulli) ed è stato effettuato il registro della geometria secondo specifica. In questo caso, la misurazione del rapporto di compressione evidenzia un forte scostamento dei parametri rispetto ai valori di specifica che superano di molto i limiti di tolleranza accettabile dal motore (v. tabella 1).
∆P [kPa] | Flusso [kg/h] | rpm | ∆P [kPa] | boost | rpm | ||
Rulli in specifica | minimo | 30,0 | 87,8 | 36.220 | 120,3 | 1,41 | 99.425 |
medio | 20,0 | 110,7 | 59,5 | 1,31 | 88.973 | ||
massimo | 3,9 | 108,9 | 30,1 | 1,16 | 64.572 | ||
Rulli con altezza aumentata di 0,1 mm | minimo | 30,1 | 88,0 | 40.540 | 119,5 | 1,300 | 90.905 |
medio | 20,2 | 110,7 | 60,9 | 1,225 | 76.169 | ||
massimo | 4,0 | 109,0 | 33,5 | 1,153 | 60.442 |
tabella 1
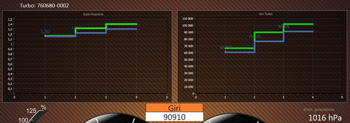
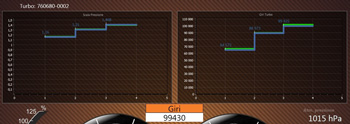
Conclusioni
In conclusione, possiamo affermare che una piccola difformità, l’altezza dei rulli della geometria per 0,1 mm., o situazioni simili, passa sicuramente inosservata in fase di assemblaggio del turbo, supera anche il test al banco di flussaggio statico ed implica sicuramente un malfunzionamento grave del motore. Essa può essere rilevata solo su un vero simulatore com’è il nostro TurboTest.
Il TurboTest presenta ancora altri vantagi rispetto ad un semplice banco di flussaggio che consistono nella possibilità di verificare la tenuta olio in condizione simili a quelle di esercizio, la possibilità di individuare la presenza del cosiddetto "fischio", la possibilità di rilevare un errore di montaggio che può causare lo sfregamento delle giranti sui carter.